Quick and Reliable Packaging Equipment Repair Solutions to Decrease Downtime
In the affordable landscape of production, the performance of packaging operations hinges on the dependability of machinery. Quick and reliable repair work solutions are vital in mitigating downtime, which can lead to substantial economic losses and functional setbacks. Understanding the value of timely interventions and the role of specialist service technicians can change just how organizations approach repair and maintenance. Browsing the myriad alternatives offered for repair service solutions can be tough. What aspects should services think about to ensure they are making the best selection for their operational needs?
Value of Timely Services
Timely repairs of packaging machines are important for maintaining operational effectiveness and reducing downtime. In the busy environment of manufacturing and product packaging, even minor breakdowns can lead to considerable delays and performance losses. Addressing problems quickly makes sure that equipments operate at their ideal capability, thus protecting the circulation of procedures.
Additionally, prompt and regular upkeep can protect against the acceleration of minor problems into significant break downs, which commonly sustain greater repair service prices and longer downtimes. A positive strategy to device fixing not only protects the stability of the devices however additionally improves the total dependability of the production line.
Additionally, prompt repairs add to the durability of product packaging machinery. Makers that are serviced promptly are less likely to experience extreme wear and tear, permitting organizations to optimize their financial investments. This is especially essential in sectors where high-speed packaging is vital, as the requirement for regular performance is critical.
Benefits of Reliable Solution Suppliers
Dependable service providers play an essential role in guaranteeing the smooth operation of product packaging machines. Their expertise not only boosts the performance of repair work but likewise adds considerably to the longevity of devices.

Additionally, a trustworthy provider supplies comprehensive support, including training and assistance for personnel on equipment operation and maintenance finest techniques. This not just encourages staff members yet also grows a society of safety and effectiveness within the organization. Generally, the advantages of involving dependable company prolong beyond instant repair services, positively affecting the entire operational operations of product packaging procedures.
Usual Product Packaging Machine Issues
In the world of packaging procedures, various concerns can endanger the effectiveness and capability of machines. One common issue is mechanical failure, typically originating from deterioration or inadequate upkeep. Elements such as motors, belts, and gears might stop working, bring about break downs that stop production. One more usual issue is misalignment, which can trigger jams and irregular product packaging, influencing item high quality and throughput.
Electrical troubles can also interfere with product packaging procedures. Faulty wiring or malfunctioning sensing units may result in irregular machine actions, causing delays and increased functional expenses. In addition, software program glitches can impede the device's shows, bring about operational inefficiencies.
Irregular product circulation is an additional important concern. This can develop from variants in product weight, dimension, or shape, which may impact the equipment's capability to take care of things precisely. Lastly, inadequate training of operators can worsen these problems, as inexperienced workers might not identify early indications of malfunction or might abuse the equipment.
Dealing with these typical product packaging device concerns promptly is important to maintaining efficiency and making certain a smooth procedure. Routine inspections and positive maintenance can considerably minimize these concerns, cultivating a trustworthy packaging atmosphere.
Tips for Reducing Downtime
To minimize downtime in product packaging procedures, executing a positive upkeep technique is essential. Routinely scheduled upkeep checks can recognize prospective concerns before they intensify, guaranteeing devices operate effectively. Establishing a routine that consists of lubrication, calibration, and evaluation of vital parts can significantly minimize the regularity of unforeseen breakdowns.
Educating staff to operate machinery appropriately and recognize early indication of malfunction can also play an important role. Equipping operators with the expertise to carry out standard troubleshooting can prevent minor problems from creating significant hold-ups. In addition, preserving a well-organized inventory of necessary extra components can useful site quicken fixings, as waiting for parts can cause extensive downtime.
Furthermore, documenting machine performance and maintenance tasks can help identify patterns and recurrent troubles, permitting for targeted treatments. Incorporating sophisticated monitoring technologies can provide real-time data, making it possible for anticipating upkeep and reducing the danger of unexpected failures.
Lastly, promoting open interaction between drivers and upkeep teams makes sure that any kind of irregularities are immediately reported and addressed. By taking these proactive measures, organizations can improve functional effectiveness and substantially decrease downtime in packaging procedures.
Choosing the Right Repair Work Solution
Selecting the suitable repair service for packaging equipments is a vital choice that can significantly affect functional webpage performance. A well-chosen solution provider makes sure that your machinery is fixed promptly, efficiently, and to the greatest requirements. Begin by reviewing the provider's experience with your details kind of packaging equipment. A specialist aware of your equipment can identify issues more properly and carry out services extra rapidly.
Following, take into consideration the company's track record. Looking for comments from other organizations within your sector can provide understandings right into dependability and high quality. Accreditations and collaborations with acknowledged devices producers can additionally show a dedication to quality.
Additionally, evaluate their action time and schedule. A company that can offer prompt assistance lessens downtime and maintains manufacturing circulation steady. It's likewise crucial to ask about service warranty and solution warranties, which can mirror the self-confidence the company has in their work.
Final Thought
To conclude, the relevance of dependable and quick product packaging machine repair service solutions can not be overemphasized, as they play a critical role in decreasing downtime and making certain operational effectiveness. By focusing on prompt fixings and picking trustworthy provider, organizations can properly deal with usual problems and preserve efficiency. Executing positive maintenance practices and spending in team training further improves the long life of product packaging equipment. Ultimately, a tactical technique to repair services fosters an extra resistant manufacturing environment.
Prompt repairs of product packaging machines are essential for maintaining functional effectiveness and reducing downtime.Furthermore, timely fixings add to the long life of packaging equipment. On the whole, the benefits of involving trusted solution suppliers expand beyond instant Read More Here fixings, positively impacting the whole operational workflow of product packaging procedures.
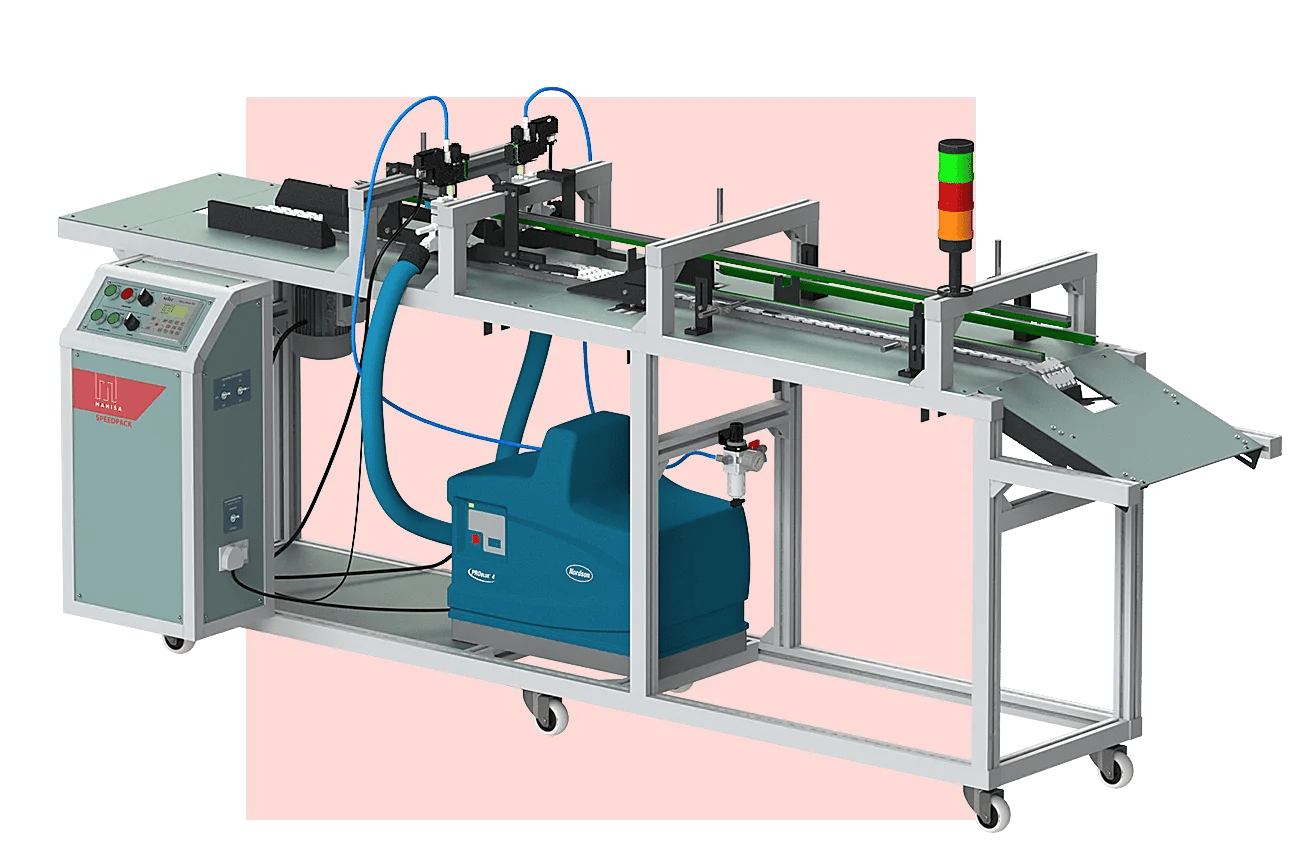